Lean Six Sigma Yellow Belt Course Overview
- Understanding of Lean Six Sigma principles and terminology
- Ability to identify and analyse process waste
- Proficiency in basic problem-solving techniques
- Skills to support larger Lean Six Sigma projects led by Green or Black Belts
Prerequisites of the Lean Six Sigma Yellow Belt Course
Who should attend this Lean Six Sigma Yellow Belt Course?
- Frontline Employees
- Supervisors
- Supply Chain Managers
- Quality Assurance Specialists
- Operations Coordinators
- Process Improvement Analysts
Course Structure
- In the first day, we will cover the essential materials needed to understand Lean Six Sigma
- The second day will cover the essential materials needed to take the Lean Six Sigma Yellow Belt exam
Lean Six Sigma Yellow Belt Course Outline
- What is Lean 6 Sigma?
- Two Parts of Lean 6 Sigma
- Focus of Lean
- Lean Temple
- Focus of Six Sigma
- Making Customers Happy
- How Do They Complement Each Other?
- Key Principles of Lean 6 Sigma
- Two Parts of Lean 6 Sigma
- Lean 6 Sigma Belts
- TKA Lean 6 Sigma Belt Structure
- Training Roadmap and Role of the Yellow Belt
- L6S Support Network
- TKA Lean 6 Sigma Belt Structure
- Processes
- Different Ways of Looking at Process Improvement
- What is a Process?
- Process Concepts
- Types of Process
- Comparing Process Types
- Different Ways of Looking at Process Improvement
- Customers, Value, and Waste
- What are Customers?
- Who Wants the Outputs?
- Tension Between the VOB and VOC
- What Do We Mean by Value?
- Path to Value
- Dealing with Values
- Muda (Waste)
- Wastes (Muda) of Lean
- Types of Demand
- Case Study Exercise
- What are Customers?
- Key Metrics
- What is DMAIC?
- Define
- Common Tools for Define Phase
- Gemba Tools
- Process Stapling
- Common Tools for Define Phase
- Measure
- Common Tools for Measure Phase
- Spaghetti (Movement/Transportation) Diagrams
- Measure Tool: Measles Charts
- Common Tools for Measure Phase
- Analyse
- Common Tools for Analyse Phase
- Common Tools for Analyse Phase
- Improve
- Common Tools for Improve Phase
- Common Tools for Improve Phase
- Control
- Common Tools for Control Phase
- Common Tools for Control Phase
- Lean Triad
- 5s
- Poka Yoke
- SMED
- 5s
- Voice of the Customer (and CTQ’s)
- Customer Chains
- Steps of VOC
- Affinity Diagrams
- Kano Diagrams
- CTQs and Requirements
- Customer Chains
- SIPOC
- What is a SIPOC?
- CSandF Web Fulfilment SIPOC
- Creating a SIPOC
- Top Tips – SIPOC
- What is a SIPOC?
- Value Stream Analysis
- Value Stream Terminology
- Process Maps
- Aim of Value Stream Mapping
- Swim Lanes and Typical Process Map Contents
- Value Stream Maps
- Headache Tablets: Value Stream Mapping
- Value Stream Terminology
- Heijunka
- Heijunka in a Nutshell
- Single Piece Flow
- Pull
- Kanban
- Three-Bin System
- Andon
- Heijunka in a Nutshell
- Variation and SPC
- Statistical Process Control (SPC)
- Two Types of Process Variation
- Red Bead Experiment
- Standard Deviation (SD) and Understanding Control Charts
- Statistical Process Control (SPC)
- Defects and Process Capability
- Conversion Table
- Process Capability
- Identifying Process Efficiency
- Conversion Table
- Key DPMO Terms
- Identifying the Root Cause(s)
- 5 Whys
- Fishbone Diagram
- 5 Whys
- Solving Problems
- Problem Solving Framework
- Prioritisation Tools
- Tools and Techniques to Generate Needed Solutions
- Problem Solving Framework
- Introduction to Kaizen
- Kaizen in a Nutshell
- Kaizen in a Business Setting
- Kaizen in a Nutshell
- Lean Teams
- Introduction to Lean Team
- Managing Progress and Demonstrating Control
- Introduction to Lean Team
What ‘s Included
World-Class Training Sessions From Experienced Instructors
Lean Six Sigma Yellow Belt Examination
Lean Six Sigma Yellow Belt Certificate
Exam
Lean Six Sigma Yellow Belt Exam
Ways to take this course
Classroom Training
Face-to-face sessions led by expert instructors, fostering interactive learning experiences and collaboration among delegates.
Online Instructor-Led Training
Live virtual classes led by experienced trainers, offering real-time interaction and guidance for optimal learning outcomes.
Online Self-Paced Training
Flexible learning at your own pace, with access to comprehensive course materials and resources available anytime, anywhere.
On-Site Training
Customised courses delivered at your location, tailored to your specific needs and scheduling preferences.
Lean Six Sigma Yellow Belt Calender
Lean Six Sigma Yellow Belt
£1495
1st January 2024
2nd January 2024
(2 days)Virtual
Lean Six Sigma Yellow Belt
£1495
2nd January 2024
3rd January 2024
(2 days)Virtual
Lean Six Sigma Yellow Belt
£1495
8th January 2024
9th January 2024
(2 days)Virtual
Lean Six Sigma Yellow Belt
£1495
13th January 2024
14th January 2024
(2 days)Virtual
Worldwide Learning Experience
These courses cater to learners worldwide, offering flexible options to fit your schedule and location.
Learning Path Towards Success
Explore
Dive into our comprehensive courses to find the best fit for your career goals.
Study
Avail our high-quality learning resources to scale up your career.
Practice
Gain hands-on experience through practical exercises, assignments and case studies.
Succeed
Achieve the skill set to attain a competitive edge in the job market.
Frequently Asked Questions
What is the difference between Yellow Belt and Green Belt?
Yellow Belts support improvement projects led by Green Belts, while Green Belts lead smaller-scale projects.
Can I pursue higher-level certifications after completing the Yellow Belt Course?
Yes, the Lean Six Sigma Yellow Belt Certification serves as a foundation for advancing to Green or Black Belt Certification.
How long is the course?
The Lean Six Sigma Yellow Belt Course is a 2-day course.
Is prior experience required to attend the Lean Six Yellow Belt Course?
No, the Yellow Belt Course is designed for beginners with no prior Lean Six Sigma experience.
What topics are covered in the Yellow Belt Course?
Topics include Lean principles, Six Sigma fundamentals, process mapping, waste identification, and basic problem-solving techniques.
What is the structure of the exam?
The Yellow Belt exam is multiple choice.
How can a Lean Six Sigma Yellow Belt Certification benefit my career?
Yellow Belt certification demonstrates your commitment to process improvement and can enhance your value to employers.
Is the Yellow Belt Certification internationally recognised?
Yes, the Yellow Belt Certification is recognised worldwide as a testament to proficiency in Lean Six Sigma principles.
Can the Yellow Belt Certification lead to job opportunities in process improvement roles?
Yes, the certification can open doors to roles such as Process Improvement Specialist, Quality Assurance Analyst, or Operations Coordinator.
How can I prepare for the Yellow Belt exam?
Reviewing course materials, practicing problem-solving techniques, and taking practice exams can help you prepare for the Yellow Belt exam.
Find Your Best Course With Us
Discover the best courses tailored to your career goals. Get in touch with our support team for expert guidance.
Explore Our Client Saying
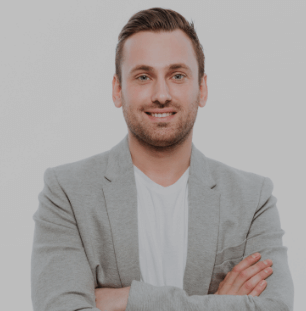
PRINCE2 Training has been an invaluable investment for us. The course was engaging, the material was excellent, and the instructors truly knew their stuff. It's not just about getting certified; it's about gaining skills that move our projects and our people forward.
Michael Carter
Project Director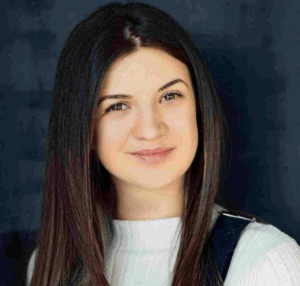
The depth and clarity of the PRINCE2 Training have surpassed all our expectations. Our team now approaches projects with greater confidence and a solid framework, leading to more predictable and successful results. We're truly grateful for the transformation.
Samantha Wong
Project Lead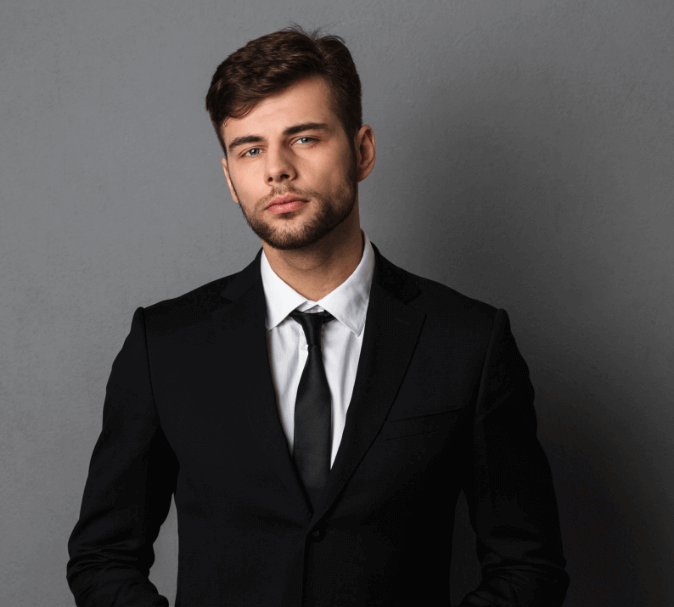
Choosing PRINCE2 Training was a pivotal decision for our team. The structured approach and practical insights have significantly improved our project delivery times and outcomes. It's clear why PRINCE2 is a leader in Project Management training!
David Patel
Senior Project Coordinator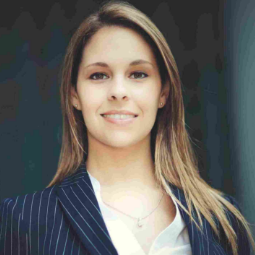
As a Project Manager, I can confidently say that registering for PRINCE2 Training was a game-changer for me. The comprehensive curriculum and practical approach gave me the tools and strategies I needed to excel in my role.
Emily Johnson
Project Manager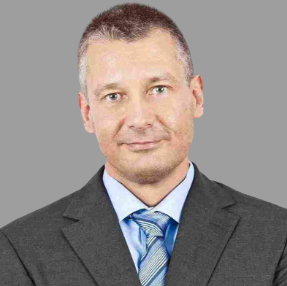
PRINCE2 Training was a game-changer for our team. The standardised approach to project management not only improved our efficiency but also enhanced collaboration and communication among team members. We're already seeing the positive impact of implementing PRINCE2 methodologies in our projects. Thank you for such a valuable learning experience!
Ada Richman
Project Governance Director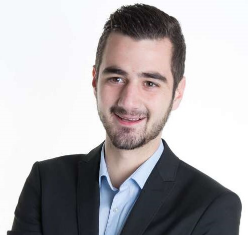
I can't say enough good things about PRINCE2 Training! The instructors were passionate about the subject matter and went above and beyond to ensure that all participants understood the material. Whether you're new to project management or looking to enhance your skills, I highly recommend investing in PRINCE2 Training.
Rod Stewart
IT Project Manager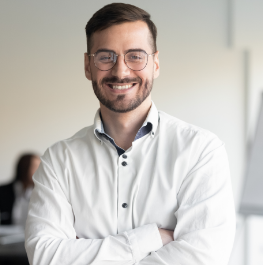
As someone with limited experience in project management, I found PRINCE2 Training to be incredibly valuable. The course content was well-structured and easy to follow, even for beginners like me. I appreciated the emphasis on practical application, which allowed me to immediately implement what I learned in my workplace.
Luca Bianchi
Program Director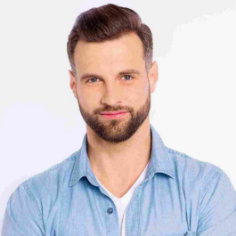
PRINCE2 Training provided me with the tools and techniques I needed to excel in my project management career. The practical exercises and real-world examples helped me apply the concepts to my job immediately. I'm grateful for the valuable skills I gained through this training program.
Henri Mitchell
Business Transformation Manager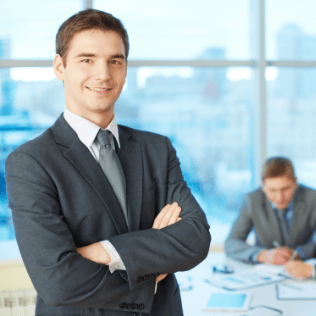
I had been looking for a comprehensive project management course, and PRINCE2 Training exceeded my expectations. The material was thorough, the instructors were engaging, and the support staff were always available to answer my questions. Thanks to PRINCE2, I feel confident tackling any project that comes my way.
Loren Crookes
Risk Management Specialist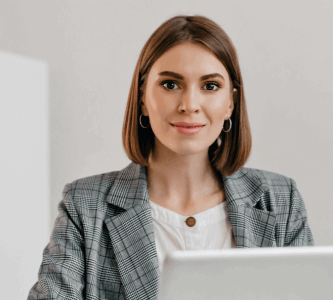
Registering for the PRINCE2 Training Was a Game-changer For Me! The Course Structure Was Well-organised, The Instructors were knowledgeable, and the hands-on approach really helped solidify my understanding of project management principles. Highly recommended!